Over the years, we have gotten many questions on which coating will be best for our customer’s use for their slide, and what are the benefits and negative aspects of each finish option. We have decided to compile some descriptions on this page in order to help educate our customers on the options that we offer. We also hope this helps with understanding what you can expect with each of the coatings and alleviate frustrations down the road for us and our customers when the coating does not perform as they expected it to.
Raw Cut/No Finish
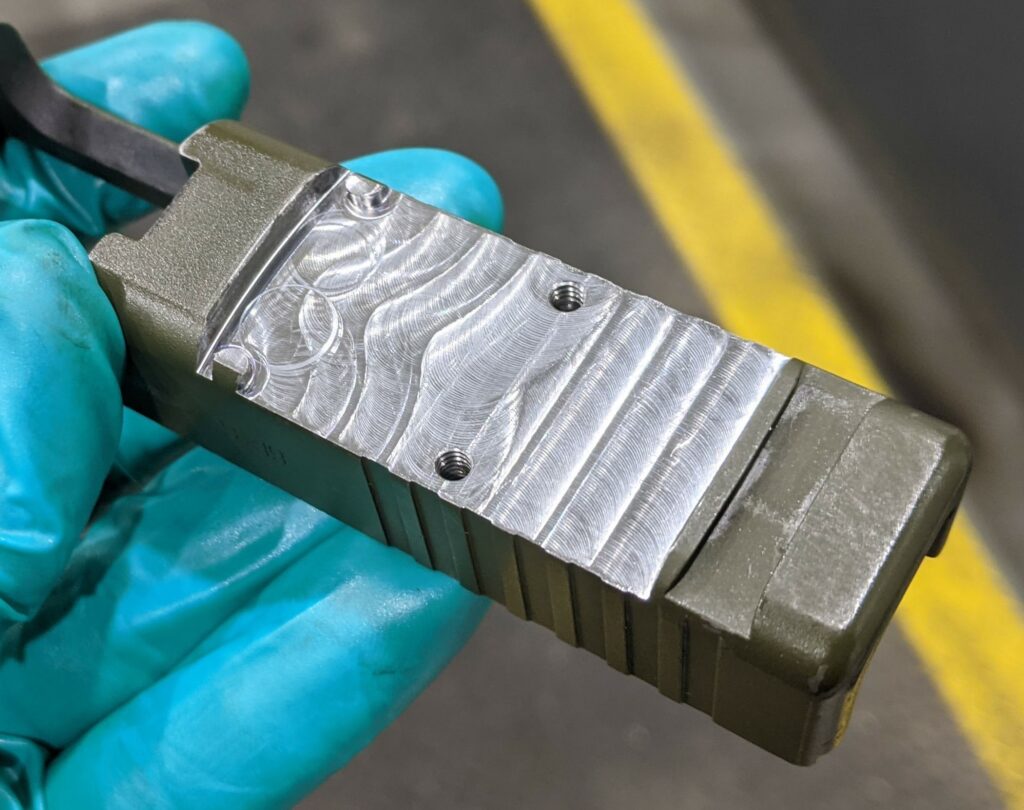
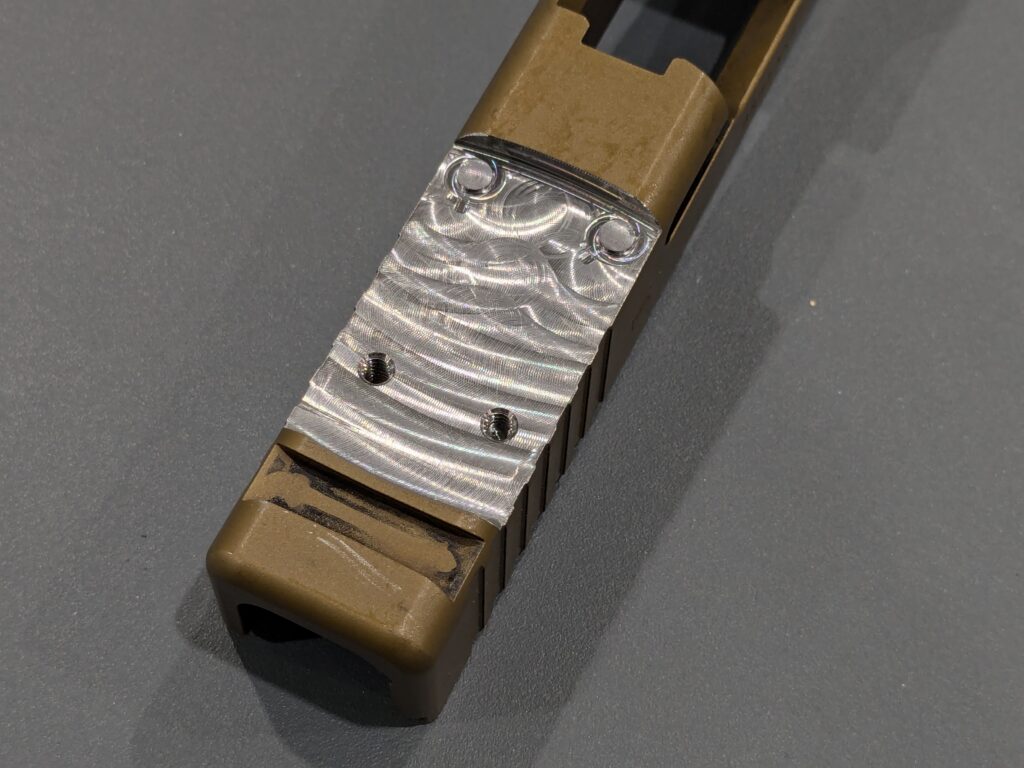
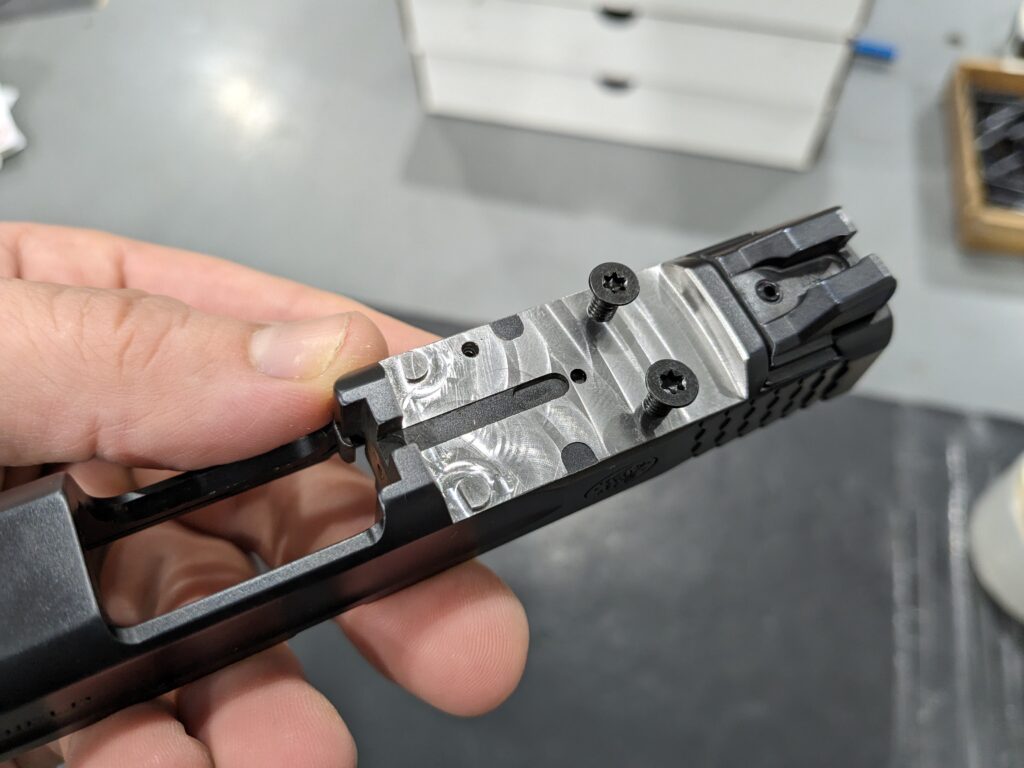
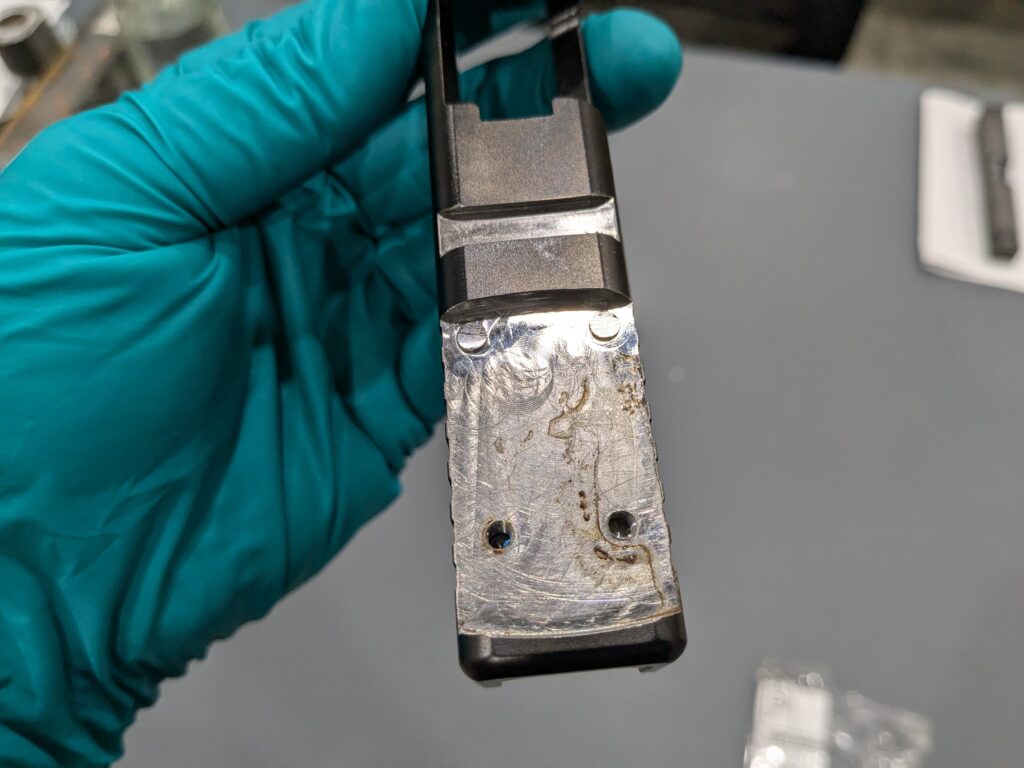
The raw machined finish is just that, uncoated. When you select this option, we assume that you will be coating the slide yourself or have someone else refinish it for you. We do not recommend to run your slide without coating the bare metal, as it will corrode over time. Some slides that are made from stainless steel (Sigs/Smith and Wessons) will do better without coating, but we still recommend a coating on those slides to ensure you do not have issues down the road. With an uncoated slide, you will obviously see machine marks from the milling process as can be seen in the 3 leftmost examples above. The picture on the right is a slide that was returned to us to get coated after it had been used for some time and you can see it is starting to rust. With the no coating option, since we are not refinishing the entire slide, there may be cosmetic marks added to your slide that were not present before. This is from the machining process and we do our best to control it, but due to it being in a CNC machine, new scratches or marks may be added to your current coating, please be aware of that when selecting this option.
Cold Blue On the Cut Area
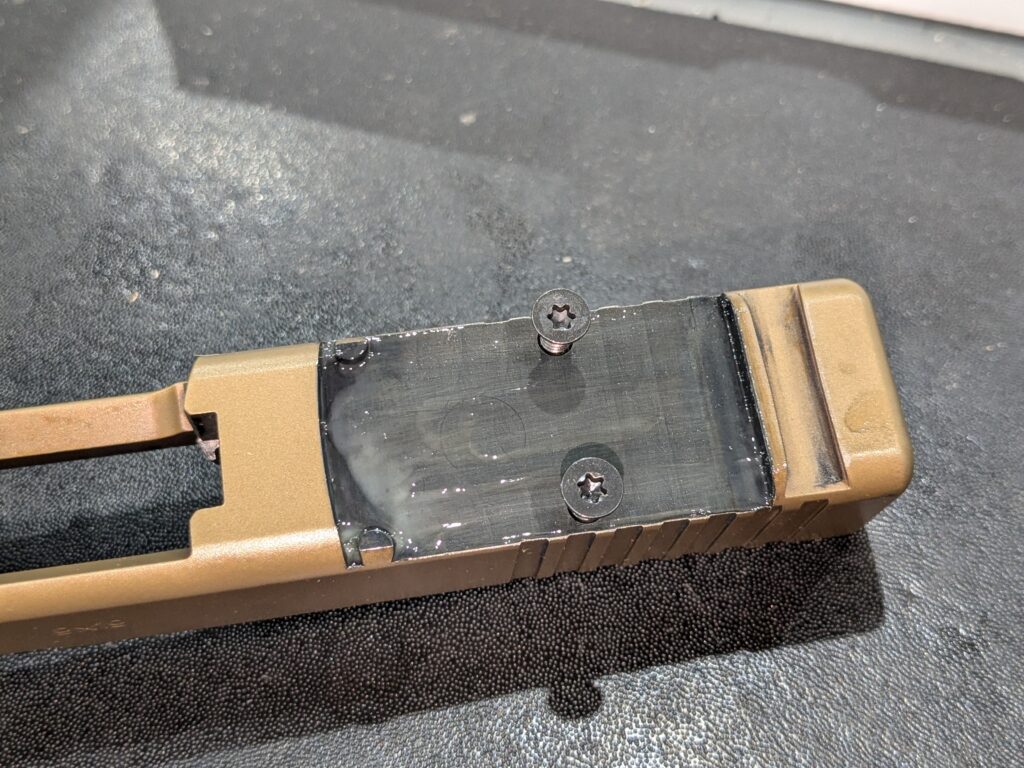
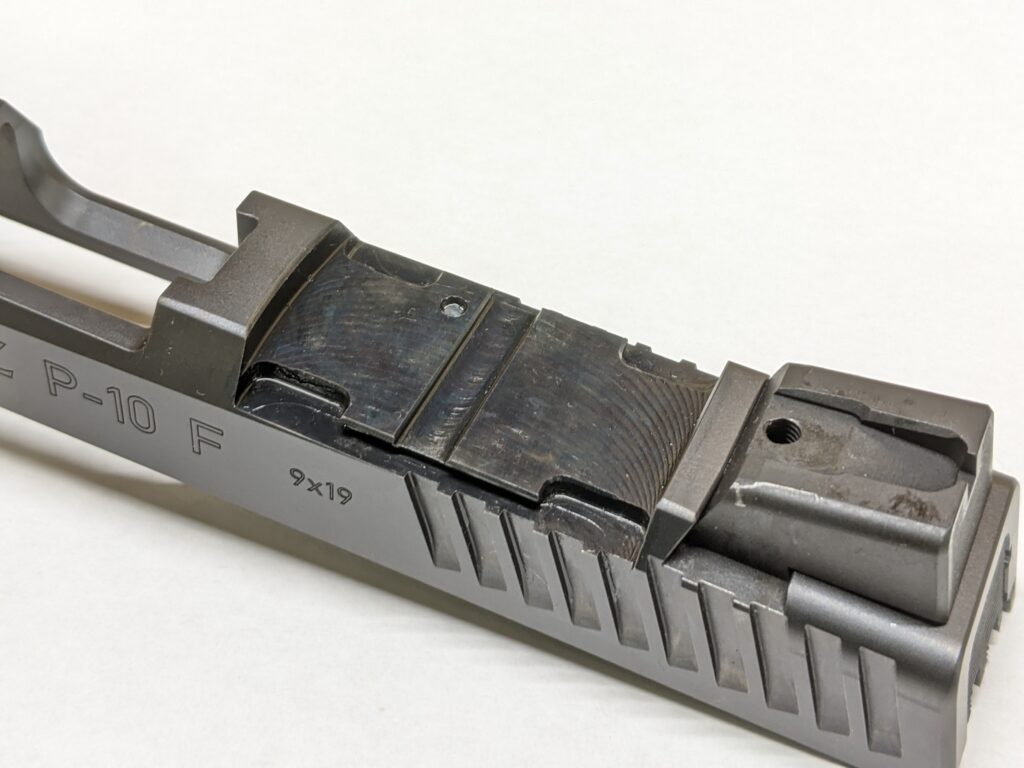
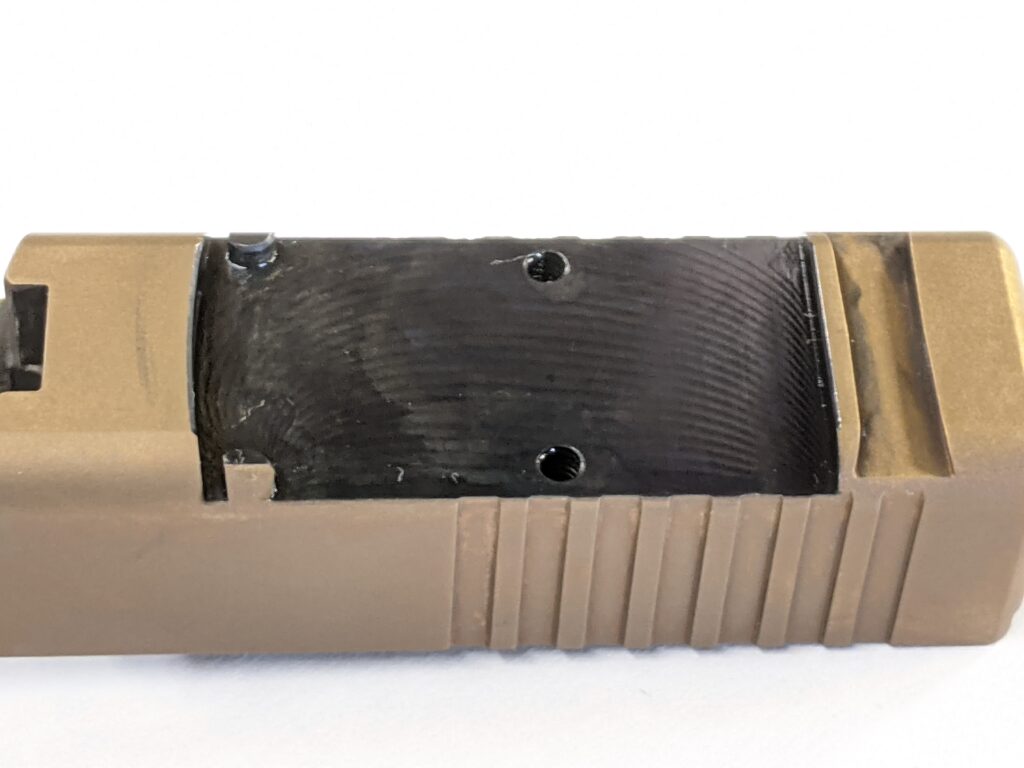
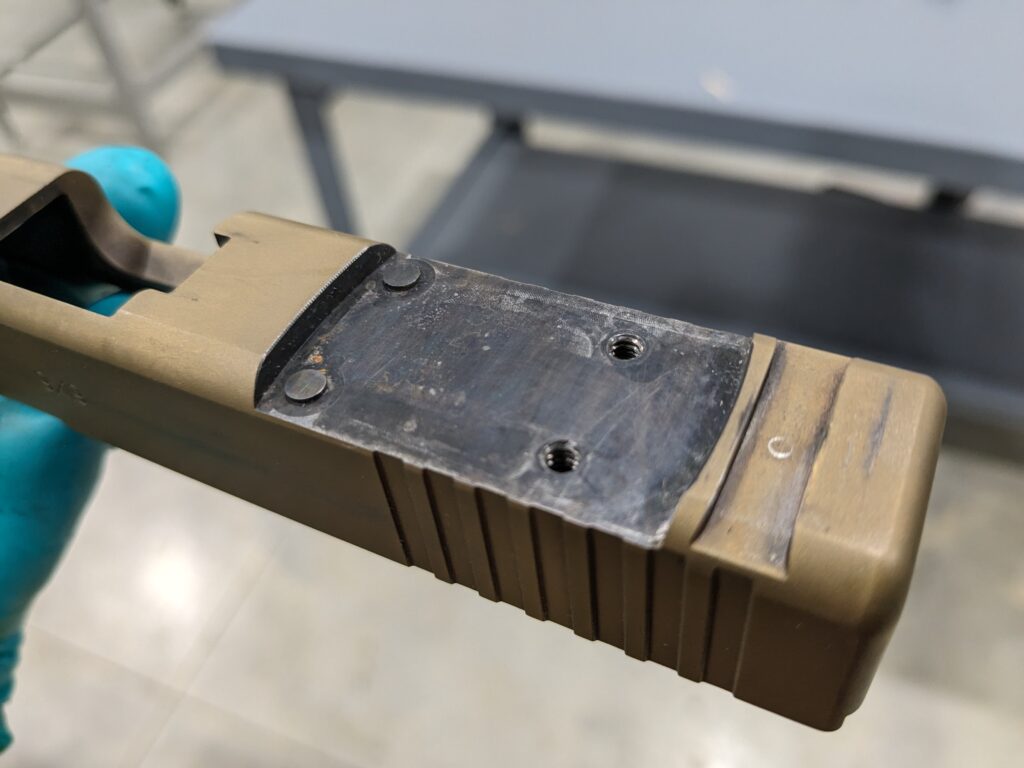
The cold blue is a finishing option that we really do not recommend, we offer it for a low cost option and because it has become somewhat of an industry standard for optic cuts. The benefit it offers is that you can refinish the area that is cut without having to refinish the entire slide. This is appeal for customers that may want to keep their factory color, finish or just want a low cost option that offers slightly better protection that no coating at all. In our experience, the cold blue is just barely a step above the no coating option. You will still see some tool marks through the coating and in some cases the cold blue will actually absorb into the tool marks better and cause the tool marks to look more prominent than that actually are. It is inconsistent in its appearance due to the metal composition and imperfections and you can expect to see irregularities in it on your slide. The blueing itself does not offer much in terms of corrosion protection, the protection comes from the oil that is applied at the end of the cold blue process. For this coating option to work effectively, you need to ensure you maintain a light coat of oil on the blued surface. We ship these slides with a light oil/grease applied to the cut area and depending on the environment that the slide will see, this oil film will need to be cleaned up and reapplied at a certain frequency. For a baseline, we recommend checking and reapplying oil when you change your optic batteries at the bare minimum. You may need to adjust your frequency to more often than that depending on how the finish is looking. For optic cuts that are a dovetail style mount (509t, Acro, MPS) the oil will need to be applied more frequently since this style optic does not really seal against the bottom of the cut like a screwed down optic will.
With the cold blue, just like the no coating option, since we are not refinishing the entire slide, there is always a chance that new cosmetic marks will be added to your slide. This is just inherent to the CNC milling process. We cannot control the coolant and chip flow within the machine while it is running. We realize that the reason some customers are opting for the cold blue is to preserve their current finish, and we do our best to ensure that happens, but some of the machining process is out of our control. Certain finishes on slides, namely cerakote and certain Glock gen 3/4 finishes are prone to showing some markings from our vice from where we hold the slide during the milling process. We do our best to alleviate this, but be aware it does still happen in some cases.
Cerakote
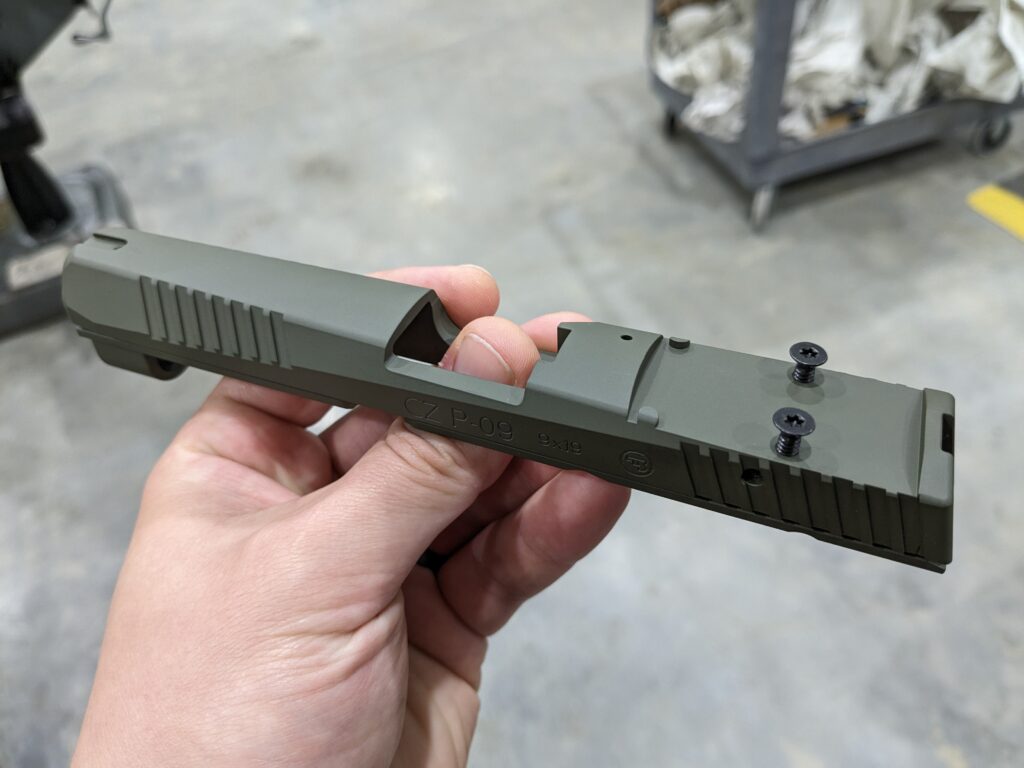
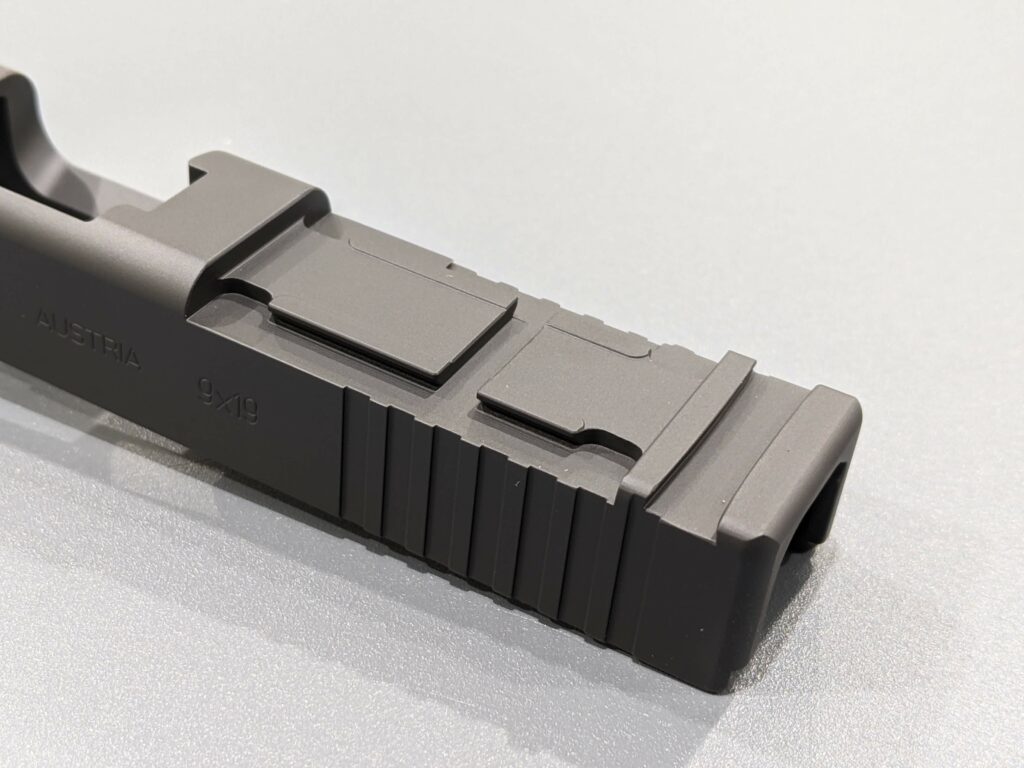
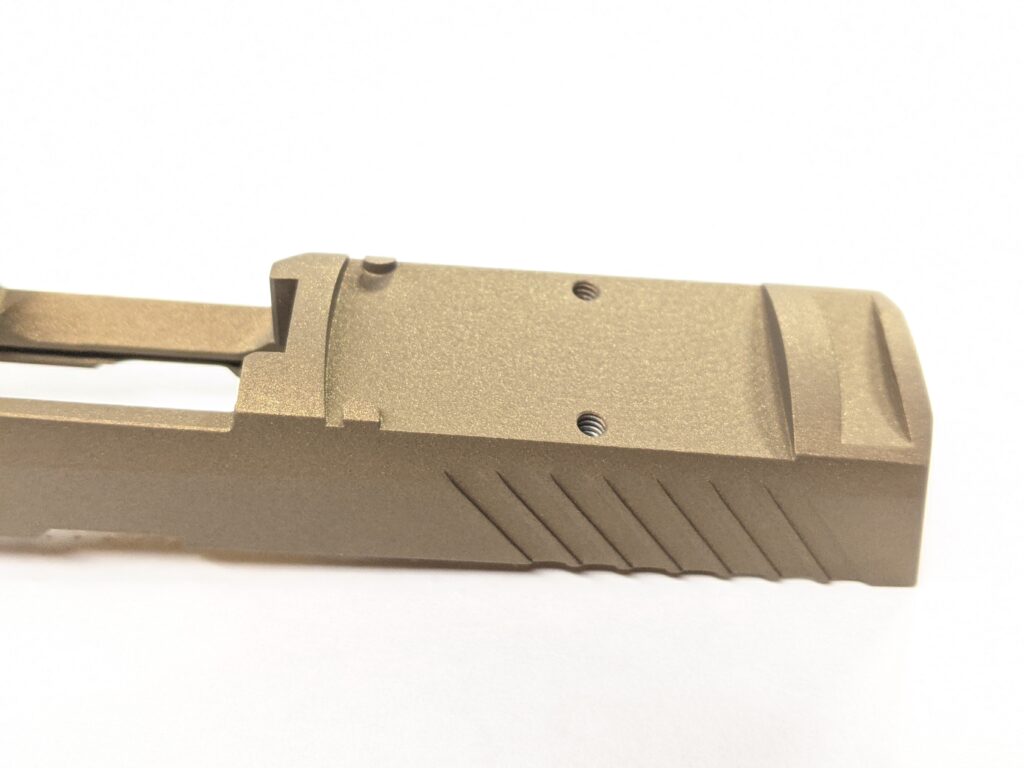
Cerakote is one of the main finishing options we offer and covers the entire slide. It gives you a fairly tough finish at a reasonable cost and offers the option to change the color of your slide. Like all things it does have its positives and negatives. In general cerakote is a great coating, but at the end of the day, it is just a painted on finish and it will behave as such. We use the oven cure type of cerakote, so it does bake into the metal a bit to help with toughness. When properly applied, cerakote will not flake off, but by abrasion it will wear over time. If you are holstering your slide, depending on your holster, wear can happen fairly quickly. When cerakote wears, it will not just wear down to the bare metal instantly, so even when it has scratches on it, it is still protected. Over time if it continues to wear in the same places, it will eventually wear down to bare metal and at that time, you should consider having it recoated.
Part of the prep process for cerakote includes blasting the slide. We blast all the of the current coating off the slide to ensure a good adhesion for the cerakote. The slide is degreased and baked off to ensure there are no machining oils or grease still on it before we apply the cerakote and then bake it to cure. By blasting the current coating off the slide entirely, this ensures that the new cerakote will not stack on top of any current coating and cause fitment issues with the slide rails/barrel. With that being said, some slides (CZ’s especially) can be tight after a fresh cerakote coating. In most cases you will want to break the slide in with 100-200 rounds to ensure consistent function. You can hand rack the slide or gently sand the rails of the slide to speed up this break in process. We are careful to go light on the rails of CZ slides, but sometimes the tolerances are just so snug that even with a light coat it can cause fitment issues. This is normal and something to be expected with the cerakote process, once you get it broken in and functioning it will not be an issue any longer.
Black Nitride
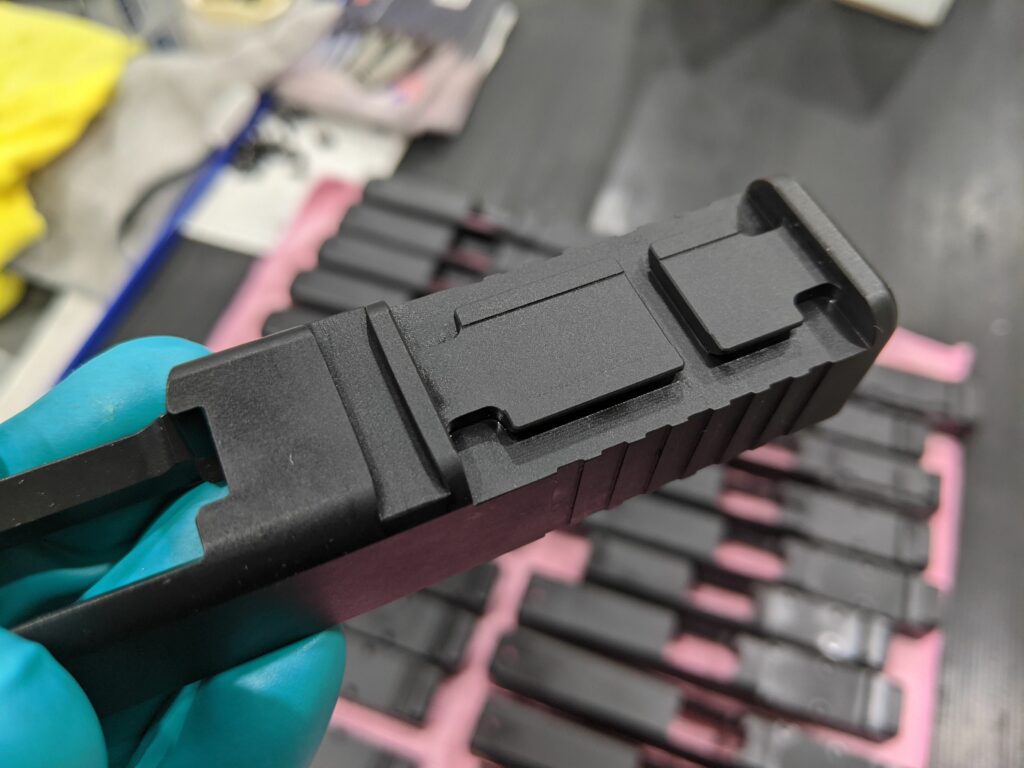
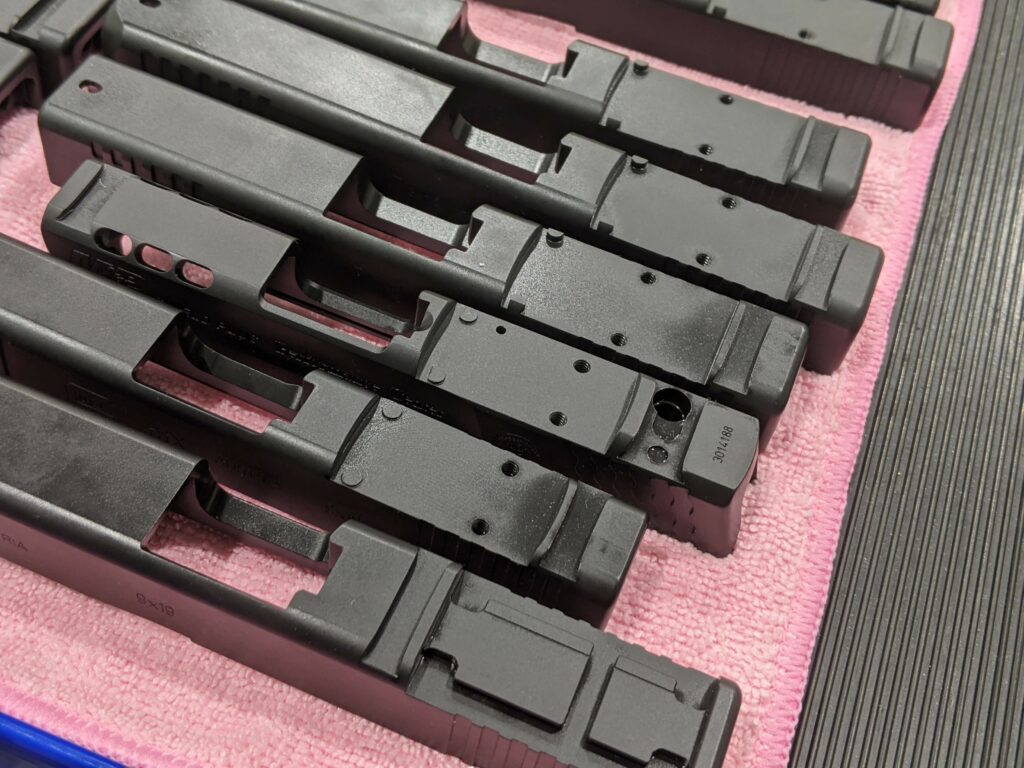
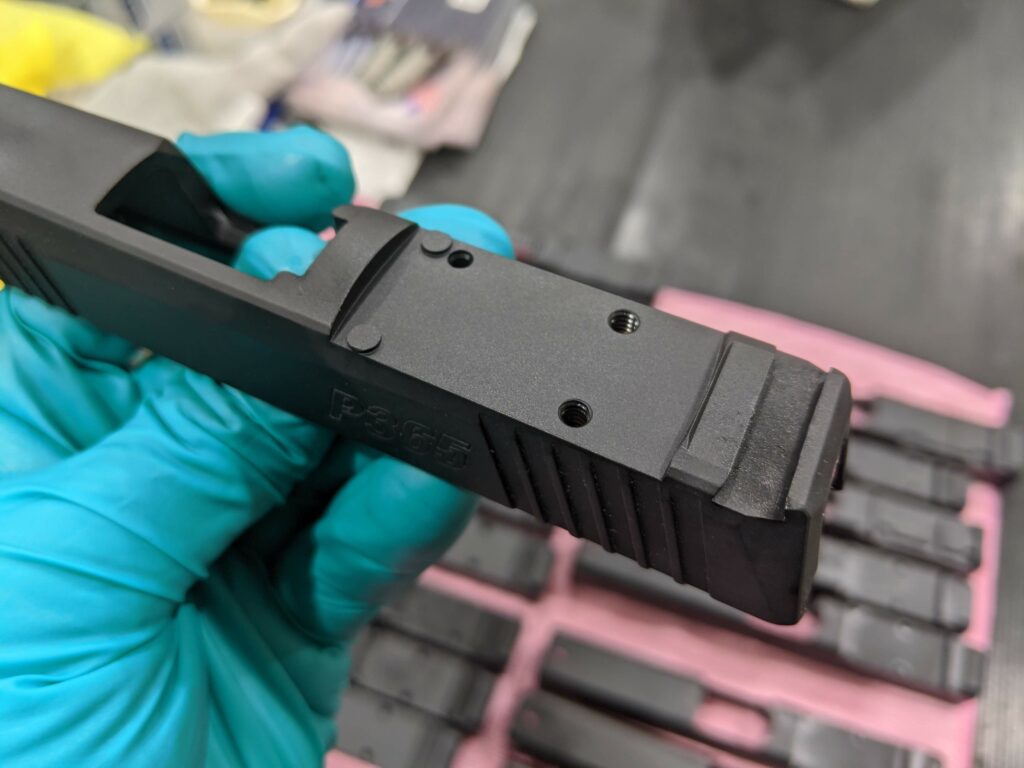
The final finish we offer is the Black Nitride. This finish will be done to the entire slide. Nitride is not a coating per se, but more of a metal refinishing option. Much like other metal refinishing options, you are not necessarily adding a coating as you are more changing the surface of the current metal.
The nitride is the toughest of the finishes we offer and is most like the OEM finish on most slides. It will hold up better than cerakote when holstered and it can take more abrasion before it will start to wear. The nitride finish adds very little thickness, so there is not typically issues with tolerances like the cerakote. Due to this, you may be able to slightly see some tool marks though the nitride. We have had instances where the nitride looked like it was wearing and starting to show scratches but it was actually the holster leaving material on the nitride and it just cleaned off with some solvent.
Overall the nitride is tough and will hold up better than any of the other finishing options, but it is still a wearable surface, so over time (depending on use/holster type) it will start showing marks like any finish will.